Mölnlycke ProcedurePak surgical trays save preparation time and boost staff efficiency and OR capacity
Thousands of hospitals in more than 60 countries depend on Mölnlycke® surgical ProcedurePak® trays, including Al Wakra Hospital in Qatar.
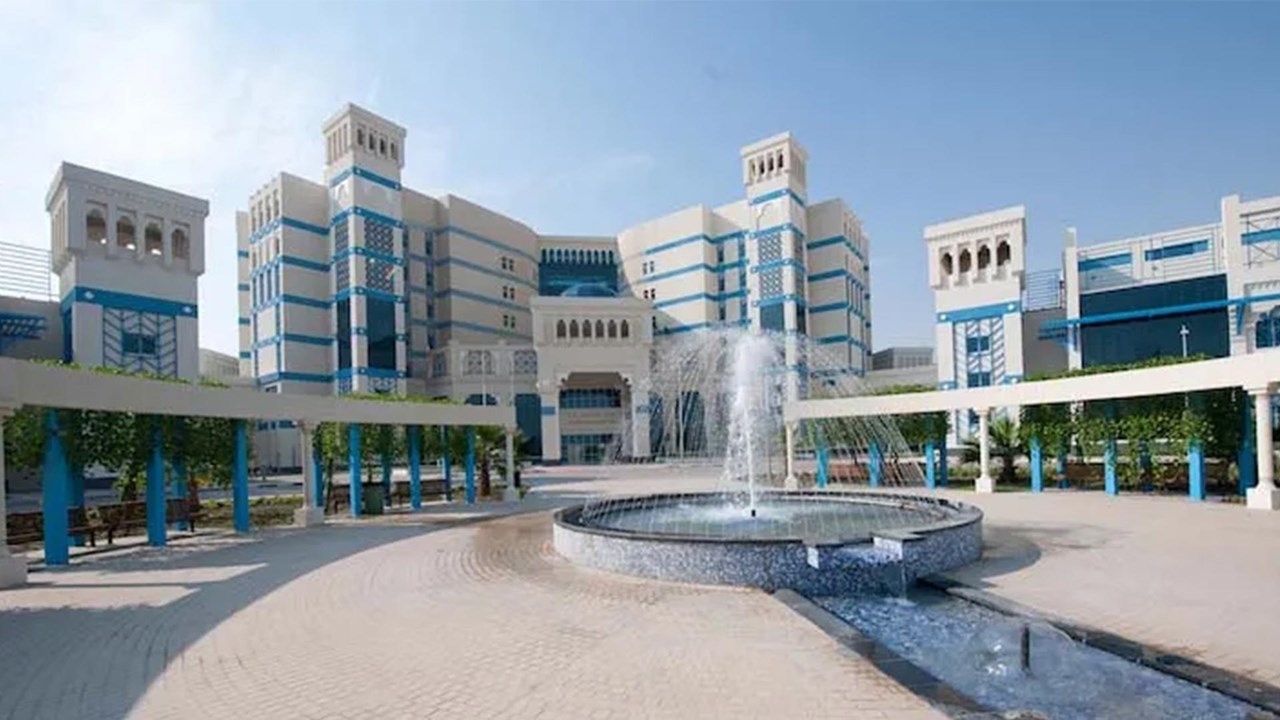
Seeking cost efficiencies and optimisation of both material inventory and OR use, ProcedurePak® trays deliver. Customised Mölnlycke® ProcedurePak® trays contribute to time savings, simplified ordering and inventory processes, and the possibility for increasing the number of surgical procedures – all providing cost control per intervention.
.
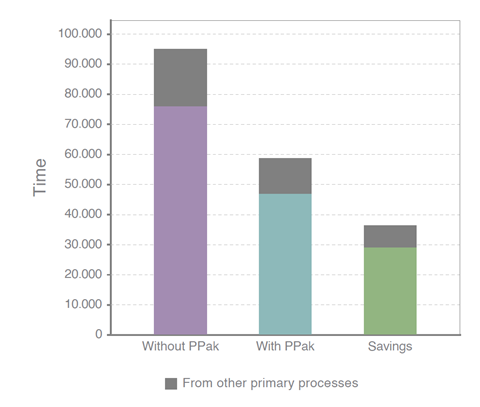
Al Wakra Hospital (AWH) is a public hospital, opened in 2012 to serve the rapidly growing towns of Al Wakra and Mesaieed. It was designed, built and equipped with the necessary staff to serve the diverse needs of the growing population in the southern regions of Qatar.
With more than 3,000 employees, including 217 doctors working across multiple medical specialities, the hospital provides a comprehensive range of high-quality healthcare services for individuals of all ages, from emergency care to internal medicine, surgery and other specialized treatment services. AWH has an estimated capacity of 325 beds, including 248 beds for general and acute patients, 77 beds for critical and intensive care and burns patients. There are also 77 short-term-stay and beds for observation.
More time to focus on patients
Thanks to Mölnlycke® ProcedurePak® trays, the full surgical workflow gains improvements and time savings for each surgical case. From the reduction in internal order and delivery time to optimising stock management, the OR supply chain is significantly simplified and streamlined. This enables time savings of 15 to 20 minutes per surgical intervention, which allows for increased OR utilisation. Time savings equals improved OR capacity, opening the door for a greater number of procedures and surgical care for more patients.
At AWH, the time savings also adds up to higher productivity overall. Each case sees a decreased cost of 50 Qatari riyal (QR). With an average number of procedures equalling 200-250, the hospital potentially saves approximately 120,000-150,000 QR yearly.
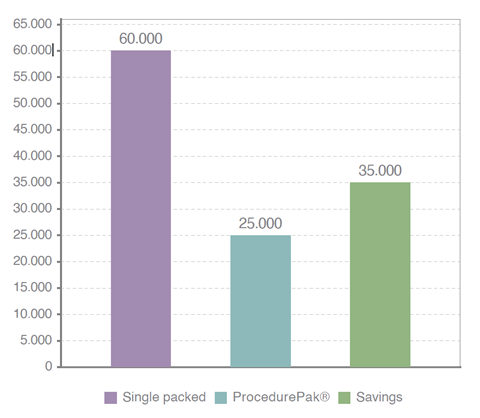
In an era when infection prevention and contamination control is a bigger concern than ever before, customised procedure trays offer additional support in reducing contamination risks.
By handling and opening fewer packages, the contamination risk is reduced significantly, helping to prevent surgical site infections (SSI).
Fewer errors, reduced waste, reduced risk = Better staff satisfaction
Mölnlycke® procedure trays are built to meet the 'one-size-does-not-fit-all' needs of individual hospitals, enabling customised tray configurations and easy ordering options through an online portal.
With Mölnlycke®, AWH has reduced the number of picking errors and scrapping costs, which in turn reduces waste and creates fewer risks during surgery prep. Staff satisfaction has been improved with ProcedurePak®, as time is saved by easing daily assignments.
Expectations exceeded
For AWH, the ProcedurePak® Value Report outcomes exceeded expectations of the end users (OT nurses) and aligned with expectations for patient safety.
To help hospitals standardise and optimise their laparoscopic procedures, Mölnlycke® offers the possibility to add single-use surgical instruments and essential surgical components to its customised ProcedurePak® trays, conveniently packed together with the laparoscopic drapes, gowns and protective clothing, gloves, antiseptics and post-op dressings. A wide range of high-quality instruments and materials is available, to include as required. A quick and easy set-up of each intervention is one of the major benefits: using Mölnlycke® ProcedurePak® trays allows up to 40% reduction in the complete preparation time, from placing the order all the way through to waste removal, and may lead to an increase of procedures per year by 18%. With fewer packages to open, the risk of infection is reduced, as well as the amount of waste to manage. The increased efficiency results in reduced product spending and lower logistics costs. Patient safety is also improved thanks to such an accurate, consistent procedure set-up. ProcedurePak® trays come with extensive support. Mölnlycke® specialists are on call to offer professional advice and customers are also offered access to the Mölnlycke® Portal. Containing a procedure tray tool, this online procedure-tray tool helps them to develop, analyse, change and estimate purchases of customised trays.
Key benefits with ProcedurePak® trays
- Frees up OR capacity to accommodate more surgical procedures
- Easier, time-saving inventory management
- Saving on preparation time
- Minimised risk of infection, with fewer packages to handle and open
- Fewer errors and risks thanks to customised ProcedurePaks and reduced picking errors
- Waste reduction because everything needed is in one package
- Gives OR staff more time and peace of mind
- Increases patient safety
- A wide choice of high-quality surgical instruments to build customized procedure trays